Digitalisaties in dental en tandtechniek hebben de afgelopen tijd niet stilgestaan en is in een enorm tempo vooruitgegaan. Het is moeilijk om deze ontwikkelingen bij te houden en daarom is het belangrijk om te beoordelen welke opties er zijn en of deze zinvol zijn voor in het lab.
3D printen is een onderdeel van digitale tandheelkunde en wordt nog steeds belangrijker. Een mooi voorbeeld is een laboratorium Uwe Aupperlen Dental Technik GmbH wat een innovatief lab is en zich bezig houdt met de nieuwste digitale technieken. Sinds de oprichting van het laboratorium in 1989 produceren zij tandprotheses. De eerste scanner kwam in 2007 in het dental lab en dit luidde een nieuw tijdperk in voor het laboratorium. Door de jaren heen is het CAD / CAM domein uitgebreid met verschillende scanners en freessystemen. Als middel om de belasting van onze freessystemen en om voor te zorgen verdere workflow in digitale processen, hebben ze besloten om te profiteren van de mogelijkheden die een 3D printer kan bieden. Het laboratorium heeft gekozen voor een open materiaal systeem van Asiga en begon met het voorgaande model de “FREEFORM PRO 2”. Nu de dag is deze vervangen door de Asiga Pro 4K, die UV-LED-licht gebruikt voor het uitharden van de materialen. De 3D print materialen van het bedrijf DETAX, zoals goedgekeurd en gevalideerd door Asiga, hebben samen de materialen zo aan elkaar afgestemd dat de eisen van de Duitse medische hulpmiddelen Act (MPG) en Medical Class 1 en 2a worden gebruikt voor de productielijn. De gebruikte materialen zijn hierin:
- Freeprint® ortho UV, voor het maken van splints, spalken en verschillende boorsjablonen en nog veel meer transparante onderdelen.
- Freeprint® tray UV, voor fabricage van individuele lepels voor beetregistratie.
- Freeprint® Cast UV, voor fabricage van gietmodellen en wax-ups.
- Freeprint® temp UV, voor fabricage van tijdelijke kronen en bruggen.
- Freeprint® model UV, voor fabricage van diverse tandheelkundig modellen.
De “Otoflash G171” post curing unit en moederboard gestuurde UV flits apparaat van NK-Optik met een beschermende gasatmosfeer is gebruikt voor de uiteindelijke (na) uitharding van geprinte objecten. Deze na hardingsapparaat is nodig om medische gecertificeerde prints te finaliseren onder stikstof nadat het reinigen met isopropanol (98% +) in een ultrasoon bad (1 + 2) heeft plaatsgevonden.
De verschillende STL-bestanden voor de respectieve 3D-printopdrachten worden gegenereerd met een open cad/cam software en scanners en in dit geval is er gekozen voor het programma van “3shape” en “Zirkozahn” systemen. Om het medische hulpmiddel “Klasse IIa” te verkrijgen, een aansprakelijkheidsclassificatie voor boormallen, röntgen en splints, is het absoluut noodzakelijk voor al deze betrokken om zich aan de voorgeschreven procedure te houden. De volgende afbeeldingen en uitleg geven een selectie van de gebieden waarin 3D-printen wordt gebruikt in het laboratorium.
Splints
De aangepaste occlusaal splints worden gemaakt in de “Zirkonzahn Bite Splint Module” en kan worden gegenereerd in ongeveer 20-40 minuten (afb. 1).
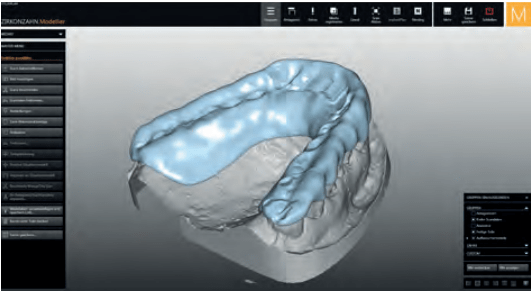
Het ontwerp kan daarna worden geplaatst in de “Asiga Composer Software” en wordt via het netwerk naar de 3D-printer verzonden en vervolgns geprint. De “Asiga Composer Software” maakt de plaatsing van individuele of meerdere print objecten zoals de splints. De grootte van het platform van de printer is bij de Freeform Pro 2 in staat om maximaal 6 parallel uitgelijnde splints te plaatsen. Dit hangt natuurlijk af van de printer, printer instellingen en de grootte van de splints of de modellen. Het aantal objecten is afhankelijk van de hoogte van de spalken en van hun plaatsingshoeken ten opzichte van het printerplatform.
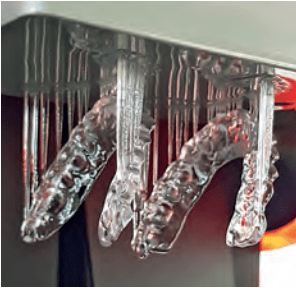
Hoe scherper de hoek met het platform wordt gekozen, hoe dikker de gepolymeriseerde lagen door het object en hoe korter de printtijd. De voltooide geprinte Freeprint® Ortho UV (DETAX) – splints worden samen met het print platform uit de printer gehaald om de deze geprinte objecten los te maken van het print platform (afb. 3).
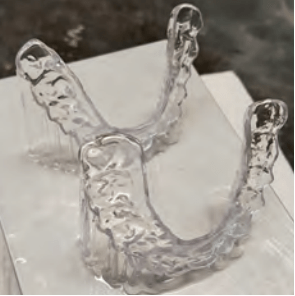
Deze zijn eenvoudig met een spatel van de drukplatform te verwijderen. Tevens worden de objecten gedurende 2 x 3 minuten (vies en schoonbad) in het ultrasoon bad gereinigd met isopropanol. Het reinigingsproces maakt de plakkerige, glanzende laag van de splints en de spalken los en worden daardoor mat (afb. 4).
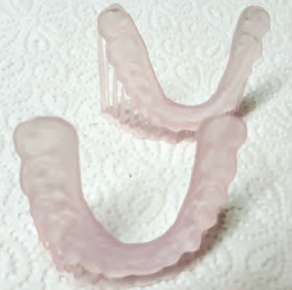
Na de laatste uitharding in “Otoflash G171” (afb. 5) kunnen de ondersteunende print support worden verwijderd. De splints worden op het model geplaatst, fijn geslepen en hoogglans gepolijst.
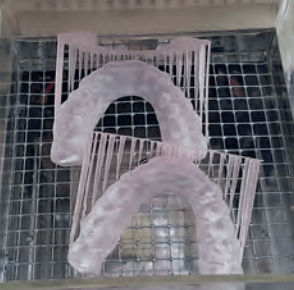
Verdere aanpassingen zijn nog mogelijk met de modelleerhars Freeform® van DETAX. De gebruikelijke roterende hulpinstrumenten, zoals polijstboortjes enz., kunnen hiervoor worden gebruikt om de splints zo af te werken. De voorgaande processen zoals post curing met de Otoflash en het schoonmaken met de Isopropyl alcohol is dermate van belang dat hoe preciezer dat gebeurt hoe makkelijker deze te polijsten is met puimsteenpoeder en het dus een doorzichtigere hoogglans splint wordt.
Röntgen- /boorsjablonen en genavigeerd boorsjablonen
Röntgen- en boorsjablonen worden gemaakt in de “3shape Implant Studio Software” met behulp van Digital Volume Tomography (DVT (DVT) (afb. 6 en 7).
Ze maken de precieze locatie mogelijk en dus ook nauwkeurig plaatsing van de geplande implantaten. De sjablonen worden op dezelfde manier geplaatst als de splints, geprint met 3d print vloeistof Freeprint® ortho UV (DETAX) (afb. 8), verwijderd van het print platform en gereinigd met de alcohol.
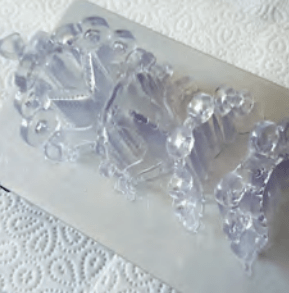
Afwerking tot een hoge glansgraad is hier niet absoluut noodzakelijk. Na definitieve uitharding en het verwijderen van de support kunnen de splints worden geplaatst op de modellen. De geselecteerde röntgen prints kunnen nu worden bijgeplaatst. kan nu worden ingevoegd de mandibulaire röntgenfoto sjabloon (afb. 9) en zo er kan een DVT worden gemaakt. Dit dient dan als de basis voor het produceren van de boormal. Nu kan de boormal worden gebruikt met de juiste geleiding (afb.10). en kunnen de implantaten worden gepland.
Lepels voor beetregistratie
De individuele lepel is geproduceerd in 3-shape met “Dental Designer” (afb. 11) in ca. 10 minuten.
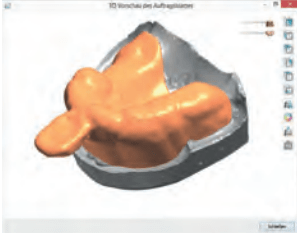
en geplaatst bij de “Asiga Composer Software” (afb. 12). Via het het netwerk worden de bestanden naar de 3D-printer gestuurd. Zodra de print klaar is met Freeprint® tray UV (DETAX), gaat het platform omhoog en kunnen de individuele lepels van het platform worden verwijderd. (afb 13).
Na het loshalen van de geprinte objecten worden deze schoongemaakt met isopropanol of cleaner in het ultrasoonbad (2x per 2 minuten) en worden de ondersteunende support structuren verwijderd waarna deze worden uitgehard met de Otoflash G171, flits uitharding apparaat, met 2 x 2000 flitsen. De lepels zijn nu klaar om te worden gepolijst indien nodig.
Maxillaire prothese
Een maxillaire prothese wordt gescand met de Zirkonzahn-scan systeem (afb. 14) en met de 3D-printer als kopie weer uitgeprint (Afb.15). Dit maakt het mogelijk een implantaat afdruk te maken terwijl tegelijkertijd het aannemen van de bestaande bijtpositie (Fig. 16).Tegelijkertijd wordt alle informatie van de gedragen prothese gebruikt bij de ontwikkelingen van een nieuwe. Figuur 17 genereert het beeld van de onbetande prothese naar de gedupliceerde geprinte prothese voor de DVT, door boorsjabloon voor de implantatie.
Pas prothese
De oorspronkelijk geproduceerde prothese is eerder vervaardigd in de 3D-printer voordat de uiteindelijke prothese wordt gefreesd (afb. 18, 19) alvorens deze kan worden geprobeerd, een try-in prothese. Op deze manier kunnen aanpassingen worden doorgevoerd, wensen van de patiënt in kaart worden gebracht en eventuele fouten opgemerkt en gecorrigeerd, zodat de definitieve prothese aan alle wensen en behoeften wordt voldaan (Afb.20).
Kronen, bruggen, uit één gegoten frames
De STL-gegevens voor de volgende gietpatroon kan worden gegenereerd in het “3shape Systeem” en “Zirkonzahn Systeem”. Een 12-delige brug is geconstrueerd met behulp van een modellering software (afb.21).
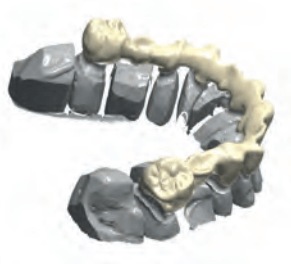
Het resulterende STL-bestand is geprint met een residu-vrije, volledig uitbrandbare gietbare 3d printhars Freeprint cast (DETAX) . Deze is geprint met support zoals eerder is beschreven (afb.22).
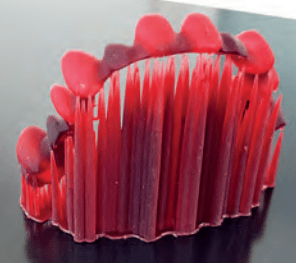
Nadat de brug is schoongemaakt in de gebruikelijke isopropyl alcohol, en het eerder beschreven cleaning en post-curing proces (afb. 23), kan het worden ingebed in de inbedmassa en worden gegoten op de conventionele manier.
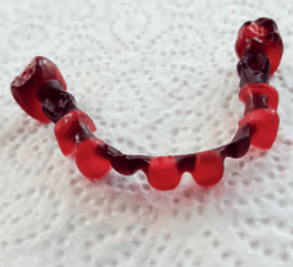
Na het afwerken van de perfect passende brug, wordt het met oxide gestraald en gereinigd en voorbereid voor keramisch opbakken (afb.24).
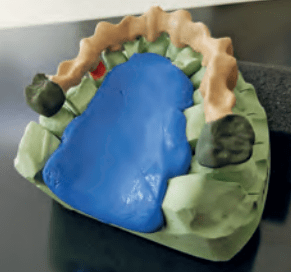
Op deze manier kunnen ook frames worden gemaakt. Frame model is ontworpen in het 3shape-model castmodule (afb.25, 26).
Zodra het bestand klaar is van ontwerp kan het worden geprint met de uitbrandbare print hars Freeprint® cast UV (DETAX), ook dit object is klaar om in te bedden en uit te gieten (afb. 27, 28).
Tijdelijke kronen, bruggen
Een brug van 13 elementen is gemaakt met behulp van de “Bridge Modeling Program” (afb. 29) en uitgeprint op de Asiga Freeform printer met Freeprint® temp UV (DETAX) (Afb.30).
Freeprint® temp UV is een klasse IIa medisch hulpmiddel. Na het steeds terugkerende en hetzelfde reinigingsproces alsook de post curing, wordt de geprinte brug, ontdaan van de vloeibare 3d printhars resten. De na harding met de Otoflash met N2 stikstof is uitermate van belang voor de medische classificatie. De supports kunnen worden verwijderd en de brug kan worden geplaatst op het model (afb.31). De brug is verwerkt met de gebruikelijke en bekende processen en dus krijgt het met polijsten krijgt een mooie glanzende afwerking. Nu de brug is klaar voor gebruik als tijdelijke prothese (afb.32). Individualisering voorafgaand aan het uiteindelijke polijsten kan uiteindelijke glans en kleur worden bereikt met behulp van het smart repair® systeem (DETAX).
Modellen en werkmodellen
Een model met uitneembare stompen kan digitaal worden vervaardigd van een digitale afdruk met behulp van de “Modellbuilder” van Zirkonzahn (uiteraard ook Exocad of 3shape). Het gemodelleerde dentale model wordt voor de productie naar de printer gestuurd en kan worden uitgeprint
met Freeprint® model UV (DETAX) of het populaire Asiga DentaModel. De volledig geprinte tandboog met de bijbehorende stompen kunnen nu worden losgemaakt van de bouwplaat, schoongemaakt volgens de bekende processen en worden geplaatst in de lichtpolymerisatie-unit de Otoflash G171 voor de uiteindelijke uitharding (afb.33). Op dezelfde tijd van het printen kunnen de kappen of onder structuren worden gefreesd uit zirkonium. Zie het afgewerkte model met bruggen (afb.34), model en brug gescheiden (afb.35).
Gebruikte systemen
- 3D printer: ASIGA Freeform PRO 2 (Asiga Max en Pro4K kunnen hier ook worden gebruikt)
- NK Optik Otoflash G 171
- Scanners: 3Shape, Zirkonzahn
Gebruikte 3D printmaterialen (DETAX)
- Freeprint® ortho UV
- Freeprint® tray UV
- Freeprint® cast UV
- Freeprint® temp UV
- Freeprint® model UV
- Freeform® smartrepair® System
Alternatieven kan worden gebruikt materialen van Keystone, KeySPlint Soft, Pro3Dure, GC en Asiga materialen. Kijk voor de materialen op onze dental site voor meer informatie en bestel direct www.sgdentalshop.com.